Today, we will teach you the basic knowledge of surface treatment for stainless steel products!
Stainless steel has unique strength, high wear resistance, superior anti-corrosion performance, and excellent characteristics such as not easily rusting. Therefore, it is widely used in the chemical industry, food machinery, electromechanical industry, environmental protection industry, household appliance industry, and home decoration and finishing industry, giving people a luxurious and noble feeling.
The application and development prospects of stainless steel will become increasingly broad, but the application and development of stainless steel largely determine the level of development of its surface treatment technology.
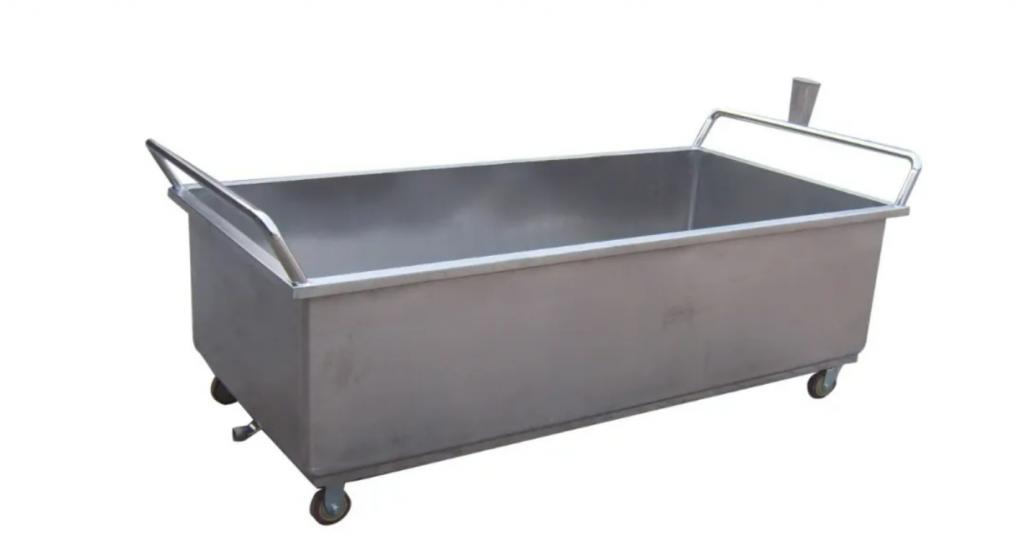
The main components of stainless steel include high-quality metal elements such as chromium (Cr), nickel (Ni), molybdenum (Mo), and titanium (Ti).
There are several commonly used surface treatment techniques for stainless steel, including: ① surface whitening treatment; ② Surface mirror gloss treatment; ③ Surface coloring treatment.
- Surface whitening treatment: During the processing of stainless steel, black oxide skin is produced by rolling, edge tying, welding, or manual surface heating treatment. This hard gray black oxide skin is mainly composed of NiCr2O4 and NiF EO4 components, which were previously removed by strong corrosion methods using hydrofluoric acid and nitric acid. But this method has high costs, pollutes the environment, is harmful to human health, has high corrosiveness, and is gradually being phased out. There are currently two main methods for treating oxide skin:
⑴ Sandblasting (shot) method: mainly using the method of spraying micro glass beads to remove the black oxide scale on the surface.
⑵ Chemical method: Use a pollution-free pickling passivation paste and a non-toxic cleaning solution with inorganic additives at room temperature for immersion washing. Thus achieving the whitening treatment of the natural color of stainless steel. After processing, it basically looks like a dull color. This method is more suitable for large and complex products.

- Surface mirror gloss treatment of stainless steel: Depending on the complexity of stainless steel products and user requirements, mechanical polishing, chemical polishing, electrochemical polishing and other methods can be used to achieve mirror gloss.
Stainless steel has excellent corrosion resistance and mechanical properties. Although its production has a long history, stainless steel has only recently entered people’s daily lives in China with the rapid improvement of living standards. In addition to medical equipment and tableware, stainless steel materials are also widely used in kitchenware, stationery, and other daily necessities. Another field that is increasingly using stainless steel is the decoration industry. Many large shopping malls and hotels use stainless steel stair handrails, stainless steel columns, stainless steel elevator doors, and car interior walls, and so on. Decorative techniques have also evolved from simple polishing to mirror polishing, embossing, and so on. Due to the inherent excellent corrosion resistance of stainless steel, it is often used without any coating and directly with its bare metal. In this way, we only see its true color – silver white, which sometimes feels a bit monotonous. So, colored stainless steel emerged.
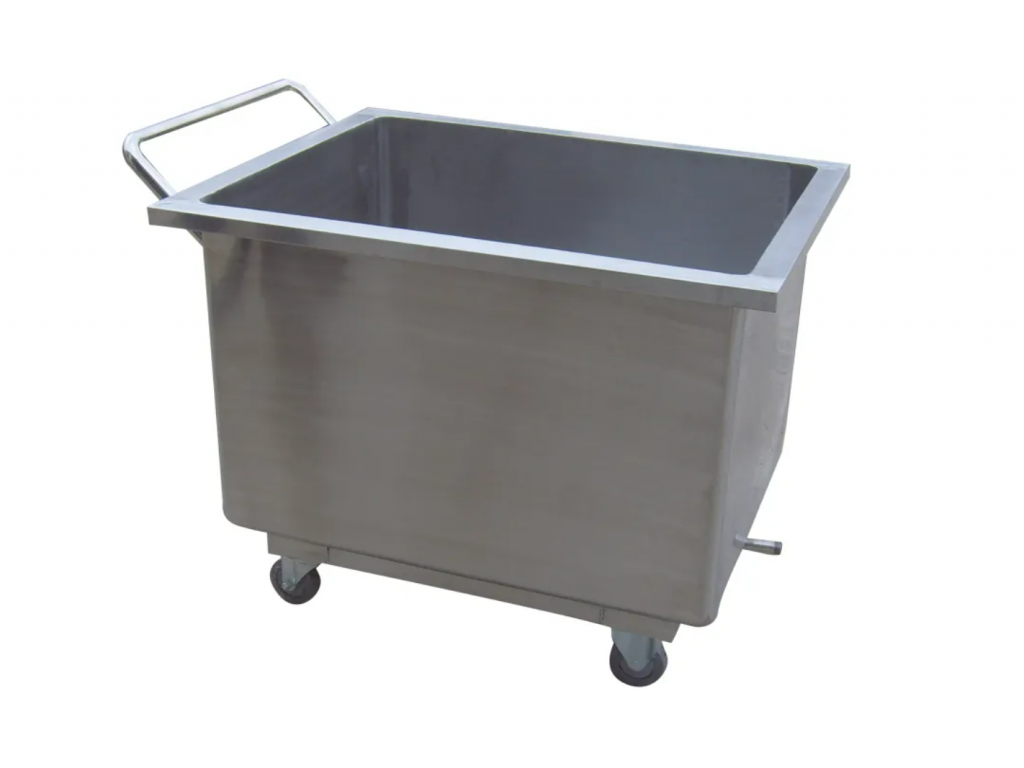
- Surface coloring treatment: Stainless steel coloring not only endows stainless steel products with various colors and increases their variety of colors, but also improves their wear resistance and corrosion resistance. There are several methods for coloring stainless steel, including:
⑴ Chemical oxidation coloring method: refers to the color of a film formed by chemical oxidation in a specific solution, including dichromate method, mixed sodium salt method, sulfurization method, acidic oxidation method, and alkaline oxidation method. INCO is commonly used, but to ensure consistent color of a batch of products, a reference electrode must be used for control.
⑵ Electrochemical coloring method: It is the color of a film formed by electrochemical oxidation in a specific solution.
⑶ Ion deposition oxide coloring method chemical method: It is to place stainless steel workpieces in a vacuum coating machine for vacuum evaporation coating. For example, watch cases and straps coated with titanium gold are usually golden in color. This method is suitable for processing large quantities of products. Due to the large investment and high cost, it is not cost-effective to produce small quantities of products.
⑷ High temperature oxidation coloring method: It is a process of immersing the workpiece in a specific molten salt to maintain certain process parameters, forming a certain thickness of oxide film on the workpiece, and presenting various colors.
Gas phase cracking coloring method: relatively complex and less commonly used in industry.
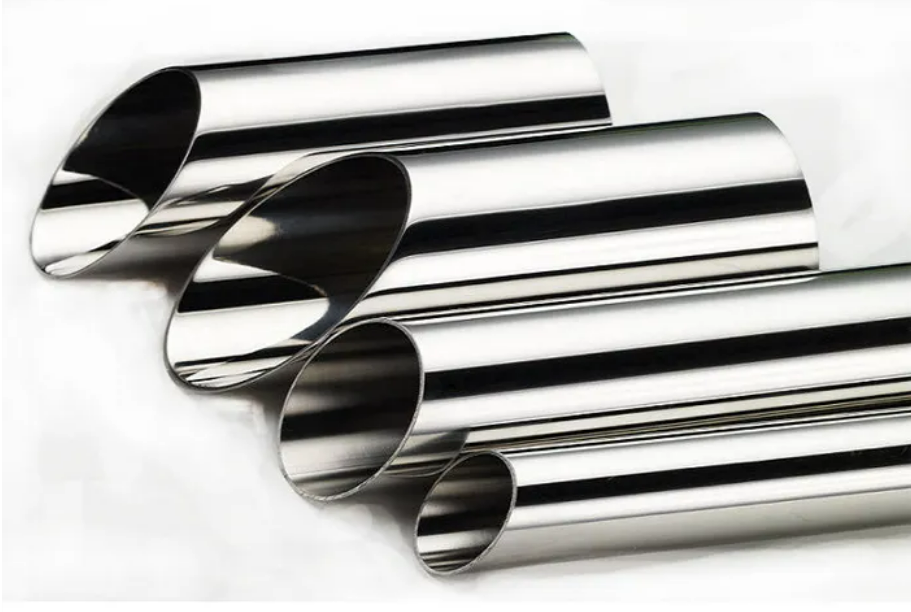
The specific method used for stainless steel surface treatment in practice should be based on the product structure, material, and different requirements for the surface, and the appropriate method should be selected for treatment.
In the past, surface treatment of stainless steel only achieved aesthetic effects, but now it can better meet the requirements of process quality. For example, fields such as biotechnology, medical devices, and food applications have high requirements for the inner and outer surfaces of stainless steel, leading to various innovative surface treatment methods. High quality standards are our lifelong pursuit.